Wdrożenie systemów zarządzania flotą w parze z rozwiązaniami IoT daje zaskakująco dużo korzyści – od optymalizacji eksploatacji wózków po zwiększenie płynności procesów oraz bezpieczeństwa pracy operatorów. Tak w każdym razie wynika z przykładu zakładu Denso Group w San Salvo.
Denso Group to pochodzący z Japonii, działający globalnie producent zaawansowanych technologicznie komponentów dla branży automotive: od systemów kontroli silnika i układu napędowego przez czujniki do nowoczesnych rozwiązań dla bezpieczeństwa aż po komponenty układu klimatyzacji i silniczki napędzające wycieraczki. Z przeszło 200 zakładami rozsianymi po całym świecie, 170 tysiącami pracowników i ponad 50 miliardami dolarów rocznego przychodu konsorcjum jest drugim co do wielkości sprzedaży producentem komponentów dla przemysłu motoryzacyjnego. Chcąc zwiększyć wydajność i bezpieczeństwo pracy w fabryce we włoskim San Salvo, Denso zdecydowało się na gruntowną modernizacją floty transportu wewnętrznego.
Charakterystyka obiektu
Spółka Denso Manufacturing Italia SpA stała się częścią koncernu w 1999 roku, kiedy japońska centrala wykupiła większościowy pakiet włoskiej fabryki Magneti Marelli. Położony w malowniczym, nadadriatyckim miasteczku San Salvo zakład produkcji komponentów elektrycznych, rozruszników, silniczków wycieraczek, dmuchaw i wiatraków, daje zatrudnienie ponad 1,1 tys. osób i dostarcza swoje wyroby do partnerów w całej Europie – i to na coraz większą skalę. W ciągu ostatnich pięciu lat zakład zwiększył produkcję z 30 do 60 tys. sztuk dziennie. By umożliwić dalszy rozwój przedsiębiorstwa przy zachowaniu płynności pracy i bezpieczeństwa zatrudnionych osób, w 2019 roku rozbudowano i unowocześniono jego flotę intralogistyczną.
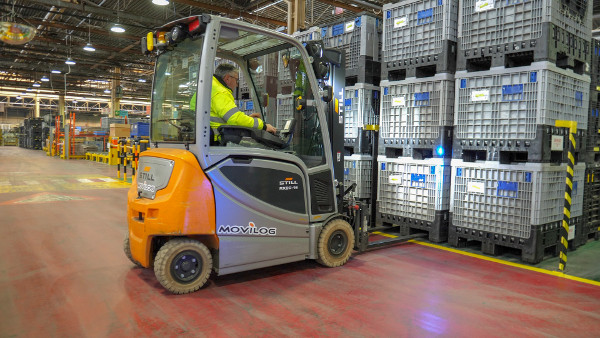
Zastosowane rozwiązanie
Nowy park maszynowy San Salvo liczy łącznie 46 nowoczesnych pojazdów. – Zaopatrzenie linii produkcyjnych oraz załadunek ciężarówek gotowymi komponentami włoskiego zakładu Denso powierzono 13 elektrycznym wózkom czołowym STILL RX 20 i RX 60 oraz 33 wózkom do kompletacji pionowej serii STILL EK-X. Wspólną cechą wszystkich zastosowanych pojazdów jest energooszczędność umożliwiająca długą pracę na jednej baterii oraz ponadprzeciętna efektywność przeładunkowa – mówi Grzegorz Kurkowski, specjalista ds. produktu STILL Polska. – Wózki wyposażono także w czujniki obciążenia ostrzegające o przekroczeniu maksymalnego udźwigu i systemy bezpieczeństwa minimalizujące ryzyko kolizji. Dodatkowo, aby zapewnić równomierną eksploatację wszystkich maszyn, wózki zintegrowano z systemem zarządzania flotą STILL FleetManager 4.x., automatycznie ewidencjonującym liczbę roboczogodzin oraz długość pokonanych tras – wymienia Kurkowski. Ciekawą innowacją jest także system automatycznego powiadamiania serwisu w przypadku awarii oraz wprowadzenie cyfrowych list kontrolnych. Dzięki ich wdrożeniu uruchomienie wózka nie jest możliwe dopóki nie sprawdzi się sprawności wszystkich najważniejszych funkcji.

Efekty wdrożenia
– Bezpieczeństwo to nasz kluczowy priorytet – mówi Ivan Rosati, starszy menadżer zakładu.
– W naszych dążeniach do osiągnięcia maksymalnej wydajności modernizacja floty okazała się cenną okazją do integracji procesów intralogistycznych z działaniami dla bezpieczeństwa pracy – relacjonuje. Rotacja eksploatowanych pojazdów dzięki systemowi zarządzania flotą wyklucza nadmierne użytkowanie poszczególnych wózków. Z kolei jednoznaczne przypisanie do konkretnego operatora korzystania z pojazdu w danym momencie zwiększa poczucie odpowiedzialności za poprawną eksploatację. – Dzięki programowi STILL FleetManager możemy w sposób ciągły monitorować wydajność każdego z wózków i efektywność całej floty. Systemy ograniczające ryzyko kolizji pozwoliły nam natomiast zintegrować nowoczesne rozwiązania z istniejącą infrastrukturą. Indywidualne przypisanie wózka do operatora w istotny sposób przyczynia się do codziennego praktykowania skoncentrowanej na bezpieczeństwie kultury organizacyjnej – podsumowuje Rosati.
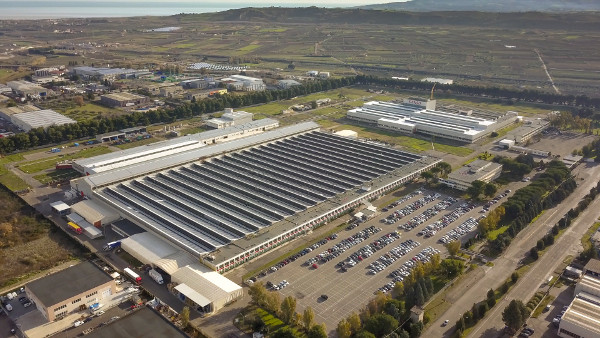
Źródło: STILL