W stale ewoluującym krajobrazie produkcji, wydajność wewnętrznych systemów transportu przemysłowego odgrywa kluczową rolę w zapewnieniu płynnych operacji w fabryce.
W dynamicznym krajobrazie nowoczesnej produkcji, wewnętrzne systemy transportowe w zakładzie odgrywają kluczową rolę w kształtowaniu wydajności operacyjnej i ogólnej produktywności. Dobrze zaprojektowany i płynnie zintegrowany system transportu wewnętrznego to nie tylko sieć przenośników i maszyn; to ucieleśnienie strategicznego podejścia do usprawnienia procesów i optymalizacji przepływu materiałów.
Niniejszy artykuł poświęcony jest dziesięciu kluczowym koncepcjom, które definiują istotę systemów transportu wewnętrznego w środowisku produkcyjnym. Od nadrzędnego znaczenia wydajności, elastyczności i bezpieczeństwa po skomplikowaną interakcję z procesami produkcyjnymi, monitorowanie w czasie rzeczywistym i skalowalność, każdy aspekt przyczynia się do skomplikowanego gobelinu solidnej i elastycznej infrastruktury transportowej. Co więcej, włączenie energooszczędnych technologii, proaktywne planowanie konserwacji i wzajemne połączenia z systemami informatycznymi (IT) wyłaniają się jako krytyczne czynniki zrównoważonego rozwoju i odporności operacyjnej. Wreszcie, artykuł analizuje kluczowe aspekty szkolenia pracowników i ergonomii, uznając niezbędną rolę wykwalifikowanej siły roboczej w zapewnieniu optymalnego funkcjonowania i długowieczności systemu transportu wewnętrznego. Ten przegląd pełni rolę kompasu dla firm produkcyjnych, które poruszają się w labiryntach logistyki wewnętrznej. Rzuca on światło na kluczowe zasady kierujące rozwojem i implementacją najnowocześniejszego systemu transportowego.
Przegląd systemów transportu wewnętrznego w zakładzie produkcyjnym
We wstępie do niniejszego raportu wymieniamy 10 najważniejszych czynników, które menedżerowie muszą wziąć pod uwagę przy wdrażaniu i zarządzaniu systemem przenośników w środowisku produkcyjnym. Następnie omówimy najważniejsze systemy fizyczne, takie jak typy taśm przenośnikowych, roboty mobilne i kwestie związane z konserwacją.
Dziesięć najważniejszych czynników, które należy wziąć pod uwagę podczas zarządzania i wdrażania systemu transportu wewnętrznego
1. Wydajność. Skuteczny wewnętrzny system logistyczny i transportowy powinien stawiać na wydajność, minimalizując czas przestojów i optymalizując przepływ materiałów i towarów w fabryce.
2. Elastyczność. System powinien być przystosowany do zmian w wymaganiach produkcyjnych, umożliwiając łatwą rekonfigurację w celu dostosowania do zmieniających się harmonogramów produkcji i asortymentu produktów.
3. Bezpieczeństwo. Bezpieczeństwo jest najważniejsze w każdym środowisku produkcyjnym. System transportowy powinien spełniać rygorystyczne normy bezpieczeństwa, obejmujące takie funkcje, jak wykrywanie przeszkód i protokoły awaryjnego wyłączania.
4. Integracja z procesami produkcyjnymi. Płynna integracja z procesami produkcyjnymi zapewnia zsynchronizowany przepływ pracy, minimalizując opóźnienia i wąskie gardła między etapami produkcji.
5. Monitorowanie i śledzenie w czasie rzeczywistym. Możliwość monitorowania i śledzenia przepływu materiałów w czasie rzeczywistym zwiększa widoczność i umożliwia proaktywne podejmowanie decyzji, przyczyniając się do lepszego zarządzania zapasami i optymalizacji zasobów.
6. Skalowalność. W miarę ewolucji potrzeb produkcyjnych, system transportu wewnętrznego powinien być skalowalny, aby dostosować się do zmian w wielkości produkcji i układzie obiektu bez znaczących zakłóceń.
7. Efektywność energetyczna. Zrównoważony system transportu wewnętrznego powinien obejmować energooszczędne technologie, aby zminimalizować wpływ na środowisko i obniżyć koszty operacyjne w perspektywie długoterminowej.
8. Planowanie konserwacji. Proaktywne planowanie konserwacji, w tym strategie konserwacji predykcyjnej, pomaga zapobiegać nieoczekiwanym awariom, zapewniając ciągłość działania i minimalizując przestoje.
9. Łączność z systemami IT. Integracja z systemami informatycznymi (IT), w tym systemami planowania zasobów przedsiębiorstwa (ERP) i systemami realizacji produkcji (MES), ułatwia wymianę danych, umożliwiając lepsze podejmowanie decyzji i alokację zasobów.
10. Szkolenie pracowników i ergonomia. Kluczowe znaczenie mają odpowiednie programy szkoleniowe dla personelu zaangażowanego w obsługę i konserwację systemu transportowego. Ponadto system powinien być zaprojektowany z uwzględnieniem zasad ergonomii, aby zapewnić dobre samopoczucie pracowników.
Systemy przenośników taśmowych: kręgosłup szybkich, wysokonakładowych i wsadowych systemów produkcyjnych
Ilekroć myślisz o logistyce wewnętrznej w fabryce, pierwszą rzeczą, która przychodzi na myśl, są systemy przenośników taśmowych, które są podstawą logistyki wewnętrznej w nowoczesnych fabrykach. Systemy te płynnie transportują materiały i produkty na różnych etapach produkcji i znacznie ewoluowały, stając się integralną częścią wydajności i konkurencyjności operacji produkcyjnych.
Systemy przenośników taśmowych są jednymi z najstarszych i najbardziej niezawodnych systemów transportu materiałów w fabryce. Systemy te można zintegrować z systemami wizyjnymi, czujnikami opartymi na IIoT oraz innymi systemami automatyki i IT, aby w pełni zarządzać materiałami lub produktami przepływającymi przez linię produkcyjną. Przenośniki taśmowe mają zasadnicze znaczenie dla funkcji zarządzania logistyką w wielu firmach produkcyjnych, więc porozmawiajmy o różnych typach systemów przenośników taśmowych, a także o ich funkcjonalności, aby określić, które systemy są odpowiednie dla Twojej firmy.
Funkcje i rodzaje systemów przenośników taśmowych
Systemy przenośników taśmowych pełnią różnorodne funkcje w logistyce wewnętrznej, w tym przemieszczanie surowców, produktów w toku i wyrobów gotowych. Można je podzielić na różne typy, takie jak przenośniki rolkowe, przenośniki taśmowe i przenośniki podwieszane, z których każdy jest dostosowany do określonych wymagań operacyjnych. Przenośniki rolkowe, na przykład, są idealne do przenoszenia ciężkich ładunków, podczas gdy przenośniki taśmowe doskonale sprawdzają się w precyzyjnym transporcie mniejszych przedmiotów. Pełna lista systemów przenośników taśmowych byłaby zbyt długa, aby ją tutaj wymienić, ponieważ większość systemów jest dostosowywana do konkretnych potrzeb firmy i przenoszonych produktów. Poniżej znajduje się lista niektórych popularnych typów systemów przenośników taśmowych:
1. Płaskie przenośniki taśmowe
– Podstawowe, płaskie przenośniki taśmowe do ogólnego transportu materiałów
2. Modułowe przenośniki taśmowe
– Taśmy składające się z pojedynczych modułów zapewniających elastyczność i łatwą wymianę
3. Przenośniki taśmowe z wypustkami
– Taśmy z wypustkami lub profilami ułatwiającymi przenoszenie materiałów pod kątem nachylenia lub spadku
4. Przenośniki taśmowe pochyłe/opadające
– Zaprojektowane do przenoszenia materiałów w górę lub w dół zboczy
5. Przenośniki taśmowe korytowe
– Taśma z podniesionymi krawędziami w celu zatrzymania materiału i zapobiegania jego rozsypywaniu
6. Systemy przenośników rurowych
– Zamknięty system przenośników taśmowych do transportu materiałów w kształcie rur, zapewniający ochronę środowiska i zapobiegający rozsypywaniu
7. Przenośniki kubełkowe
– Łyżki lub kubełki przymocowane do obracającej się taśmy do pionowego lub pochyłego transportu materiałów sypkich
8. Przenośniki łańcuchowo-taśmowe
– Taśmy wykonane z zazębiających się łańcuchów do ciężkich zastosowań
9. Przenośniki rolkowe
– Rolki używane do podtrzymywania i przesuwania taśmy
10. Przenośniki listwowe
– Listwy lub płyty używane jako ruchoma powierzchnia dla ciężkich lub nieregularnie ukształtowanych przedmiotów
11. Przenośniki z siatki drucianej
– Taśmy wykonane z połączonych ze sobą drutów metalowych, odpowiednie do zastosowań wysokotemperaturowych
12. Przenośniki podwieszane
– Podwieszane pod sufitem, używane do transportu elementów w procesie produkcyjnym
13. Przenośniki rolkowe napędzane
– Rolki są napędzane w celu przemieszczania elementów
14. Grawitacyjne przenośniki rolkowe
– Polegają na sile grawitacji przy przemieszczaniu przedmiotów w dół zbocza
15. Przenośniki taśmowo-rolkowe
– Łączy w sobie zalety przenośnika taśmowego i rolkowego
16. Przenośniki ślizgowe
– Podobne do przenośników rolkowych, ale wykorzystują gładką powierzchnię taśmy
17. Magnetyczne przenośniki taśmowe
– Wykorzystuje magnesy do przenoszenia materiałów żelaznych
18. Przenośniki wibracyjne
– Wykorzystują wibracje do przenoszenia materiałów
19. Przenośniki pneumatyczne
– Wykorzystują ciśnienie powietrza do przenoszenia materiałów przez system
20. Przenośniki śrubowe
– Wykorzystuje obracające się spiralne ostrze śrubowe do przenoszenia materiałów sypkich
21. Przenośniki elastyczne
– Przenośniki, które można wyginać lub zakrzywiać w celu poruszania się w ciasnych przestrzeniach
22. Przenośniki magnetyczne bez pasów
– Wykorzystują magnesy i pola magnetyczne do transportu materiałów.
To tylko kilka przykładów, a wybór systemu przenośników zależy od takich czynników, jak rodzaj transportowanego materiału, odległość, jaką musi pokonać, wymagana prędkość i konkretne wymagania dotyczące zastosowania.
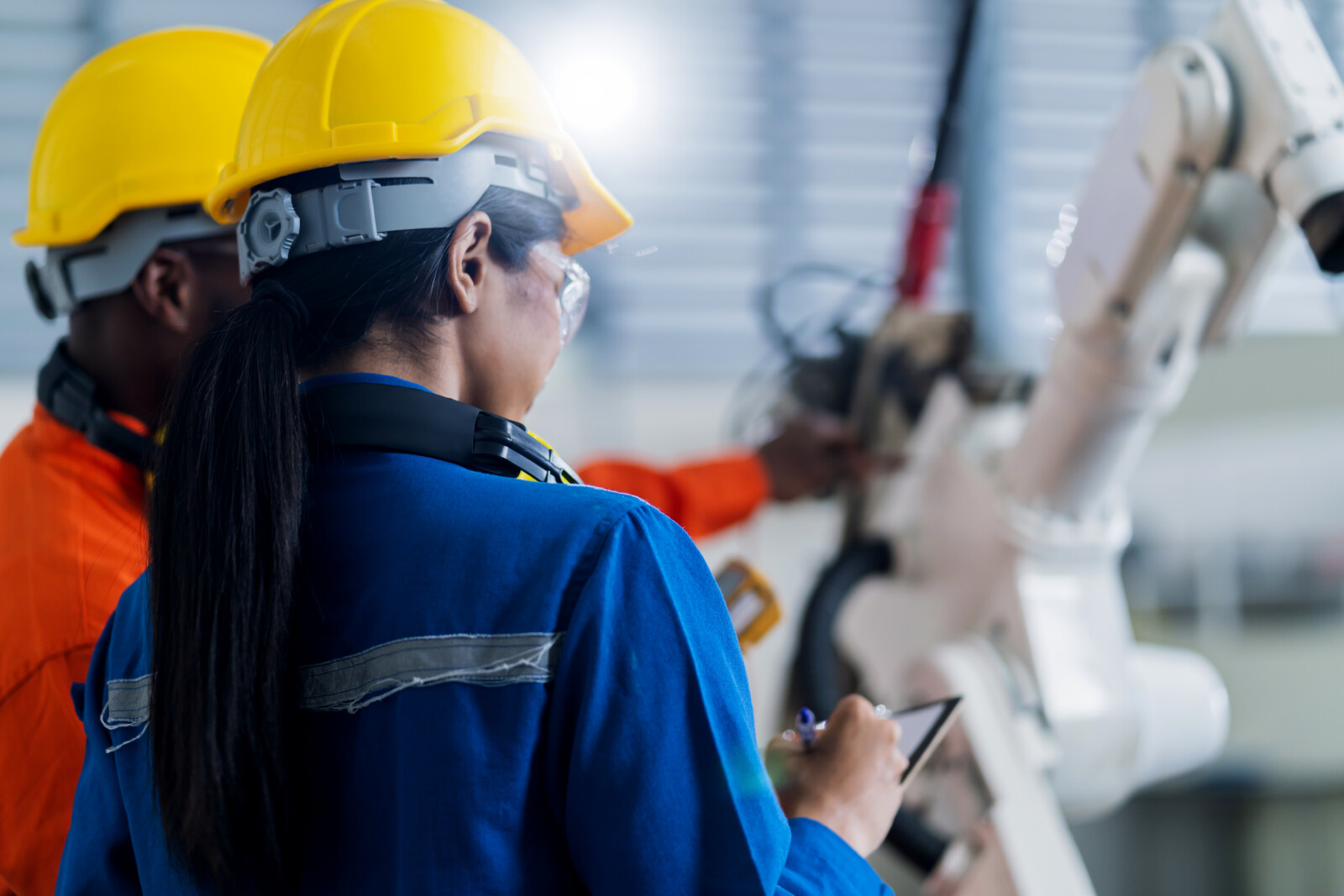
Zalety systemów przenośników taśmowych
Jedną z głównych zalet systemów przenośników taśmowych jest ich zdolność do usprawniania przepływu materiałów, zmniejszając ręczną obsługę i związane z tym koszty pracy. Systemy te zwiększają wydajność poprzez utrzymanie ciągłego i spójnego przepływu produkcji, minimalizując ryzyko powstawania wąskich gardeł. Dodatkowo, przenośniki taśmowe przyczyniają się do poprawy bezpieczeństwa, zmniejszając potrzebę ręcznego transportu ciężkich lub nieporęcznych przedmiotów, tym samym zmniejszając ryzyko obrażeń w miejscu pracy.
Podczas gdy systemy przenośników taśmowych oferują liczne korzyści, mogą pojawić się wyzwania, takie jak potencjalne awarie lub potrzeba konserwacji. Jednak proaktywne planowanie konserwacji, obejmujące strategie konserwacji predykcyjnej, może złagodzić te wyzwania. Szybkie rozwiązywanie problemów i integracja inteligentnych technologii monitorowania w czasie rzeczywistym może dodatkowo zwiększyć niezawodność i odporność systemów przenośników taśmowych.
Pojawiające się trendy
Przyszłość systemów przenośników taśmowych w logistyce wewnętrznej charakteryzuje się kilkoma ekscytującymi trendami. Aplikacje Przemysłu 4.0, takie jak integracja czujników i technologii IoT, umożliwiają monitorowanie danych w czasie rzeczywistym i analizę predykcyjną, ułatwiając podejmowanie mądrzejszych decyzji i ograniczając przestoje. Ponadto postępy w projektowaniu przenośników koncentrują się na modułowości i elastyczności, umożliwiając łatwą adaptację do zmieniających się potrzeb produkcyjnych i układów. Ponieważ zrównoważony rozwój staje się centralnym punktem w produkcji, energooszczędne systemy przenośników zyskują na znaczeniu, dostosowując się do globalnych wysiłków na rzecz zmniejszenia wpływu na środowisko.
Podsumowując, systemy przenośników taśmowych odgrywają kluczową rolę w optymalizacji wewnętrznej logistyki w fabrykach. Ich ewolucja od podstawowego transportu materiałów do zaawansowanych systemów opartych na technologii odzwierciedla ciągłe zaangażowanie w zwiększanie wydajności, bezpieczeństwa i zrównoważonego rozwoju w procesach produkcyjnych. W miarę ewolucji tych systemów, fabryki mogą spodziewać się jeszcze większych postępów, co dodatkowo przyczyni się do płynnego i wydajnego przepływu materiałów w całym cyklu produkcyjnym.
Technologia transportu wewnętrznego w ostatnich latach rozwija się bardzo szybko. Świadomość przedsiębiorców w Polsce rośnie i zdecydowanie chętniej szukają rozwiązań, które pomogą im w znalezieniu oszczędności przy procesach logistycznych. Zwiększenie efektywności oraz dbanie o zdrowie pracownika bezpośrednio przyczynia się do utrzymania konkurencyjności przedsiębiorstwa.
Polskie firmy zdają sobie sprawę z konieczności dostosowania się do nowoczesnych trendów w zakresie transportu wewnętrznego. Jest to szczególnie zauważalne, gdy przeanalizujemy różnorodność sektorów, które zgłaszają się po ofertę dotyczącą przemysłowych elektrycznych pojazdów wolnobieżnych marki Frugal. Pełna automatyzacja jest bardzo droga i nie wszystkie firmy mogą sobie na nią pozwolić, natomiast są rozwiązania na rynku, które stosunkowo niewielkim kosztem bardzo pozytywnie wpływają na logistykę wewnątrz-zakładową. Takim rozwiązaniem są między innymi elektryczne pojazdy wolnobieżne Frugal, które są prostsze konstrukcyjnie, posiadają nawet 80% mniej części ruchomych od pojazdu napędzanego silnikiem spalinowym, co znacznie zmniejsza wydatki eksploatacyjne i serwisowe. Ponadto, istnieje możliwość jednorazowej amortyzacji. Oznacza to, że po zakupie pojazdu, w przeciwieństwie do klasycznego samochodu, przedsiębiorcy mają możliwość odliczenia pełnego podatku VAT od zakupu, co dodatkowo wspiera efektywność finansową przedsiębiorstwa.
System transportu wewnętrznego, bez którego polskie firmy nie będą w stanie skutecznie konkurować w przyszłości to przede wszystkim elektryfikacja. Urządzenia oraz pojazdy elektryczne są bardziej przyjazne środowisku, ponieważ nie emitują bezpośrednio gazów cieplarnianych ani szkodliwych substancji, a także ich eksploatacja wymaga zdecydowanie niższych nakładów finansowych. Obecnie coraz bardziej popularne stają się idee zeroemisyjności, a firmy są w pewien sposób zobowiązane do przyjmowania ekologicznych praktyk biznesowych.
Najważniejsze technologie mogą różnić się w zależności od branży, natomiast skupiają się one na rozwiązaniach, które przynoszą efektywność, elastyczność i umożliwiają szybsze osiąganie celów. Elektryczne pojazdy CARGO marki Frugal wpisują się w strategię zrównoważonego rozwoju i niskim kosztem pozwalają przyspieszyć oraz ułatwić transport. Świadomość ekologiczna i inwestycja w zielone technologie jest w dzisiejszych czasach bardzo pozytywnie odbierana przez klientów czy też kontrahentów przedsiębiorstw.
Krzysztof Piekut – Product Manager Frugal
Wzrost popularności robotów w transporcie materiałów: trendy i korzyści technologii AMV i AMR w logistyce produkcji
W stale ewoluującym krajobrazie logistyki produkcji integracja autonomicznych pojazdów mobilnych (AMV) i autonomicznych robotów mobilnych (AMR) stała się siłą transformacyjną, rewolucjonizując sposób obsługi i transportu materiałów w halach produkcyjnych. Chociaż nie są one wykorzystywane do tych samych celów, co systemy przenośników taśmowych, roboty mobilne zmieniają sposób, w jaki materiały, zapasy i produkty są przemieszczane po hali produkcyjnej. Poniżej przedstawiamy dynamiczne trendy i niezrównane korzyści związane z przyjęciem technologii AMV i AMR w środowiskach produkcyjnych:
Trendy w technologii AMV i AMR
1. Inteligentne systemy nawigacji
Wykorzystując zaawansowane algorytmy nawigacji, pojazdy AMV i AMR są coraz częściej wyposażone w inteligentne funkcje mapowania i unikania przeszkód, zapewniając płynny ruch w skomplikowanych układach produkcyjnych.
2. Robotyka współpracująca
Konwergencja technologii AMR z systemami robotów współpracujących staje się coraz bardziej widoczna, ułatwiając bezpieczne i wydajne interakcje między robotami a pracownikami na hali produkcyjnej.
3. Łączność i integracja
Widoczny jest trend w kierunku większej wzajemnej łączności, z AMV i AMR płynnie integrującymi się z innymi technologiami Przemysłu 4.0. Ten połączony ekosystem usprawnia wymianę danych w czasie rzeczywistym, umożliwiając podejmowanie bardziej świadomych decyzji w zakresie planowania logistycznego.
4. Personalizacja i zdolność adaptacji
Producenci skłaniają się ku konfigurowalnym rozwiązaniom AMV i AMR, które można łatwo dostosować do konkretnych potrzeb produkcyjnych. Trend ten zapewnia elastyczność w obsłudze różnych materiałów i dostosowywaniu się do zmieniających się wymagań produkcyjnych.
Od zwiększonej wydajności i znacznych oszczędności kosztów po przełomowe postępy w zakresie bezpieczeństwa i niezrównaną skalowalność, te autonomiczne systemy robotyki nie są jedynie narzędziami do obsługi materiałów; są architektami bardziej zwinnej, wydajnej i wzajemnie połączonej przyszłości produkcji. Poniżej wymieniliśmy pięć głównych zalet robotów mobilnych i współpracujących w obszarze obsługi materiałów:
1. Zwiększona wydajność
Roboty AMV i AMR przyczyniają się do bardziej wydajnego procesu obsługi materiałów poprzez optymalizację tras, minimalizację czasu bezczynności i ograniczenie interwencji ręcznych, ostatecznie zwiększając ogólną produktywność operacyjną.
2. Oszczędność kosztów
Wdrożenie systemów autonomicznych prowadzi do oszczędności kosztów dzięki zmniejszeniu kosztów pracy, niższemu poziomowi błędów i poprawie efektywności energetycznej. Ta efektywność finansowa jest kluczowym czynnikiem stojącym za rosnącą popularnością technologii AMV i AMR.
3. Postęp w zakresie bezpieczeństwa
Bezpieczeństwo zajmuje centralne miejsce dzięki integracji zaawansowanych czujników i algorytmów, umożliwiając pojazdom AMV i AMR bezpieczną nawigację w dynamicznych środowiskach. Promuje to bezpieczne środowisko pracy zarówno dla ludzi, jak i maszyn.
4. Skalowalność i adaptacja
W miarę ewolucji potrzeb produkcyjnych, systemy AMV i AMR wykazują się skalowalnością, łatwo dostosowując się do zmian wielkości produkcji i układu, zapewniając producentom przyszłościową inwestycję.
5. Podejmowanie decyzji w oparciu o dane
Monitorowanie w czasie rzeczywistym i analiza danych zapewniają producentom wgląd w przepływ materiałów, umożliwiając proaktywne podejmowanie decyzji, lepsze zarządzanie zapasami i optymalizację zasobów.
Nawigacja w obsłudze materiałów: kompleksowa analiza typów wózków widłowych w zakładach produkcyjnych
W dynamicznym świecie produkcji wydajny i strategiczny przepływ materiałów ma kluczowe znaczenie dla sukcesu operacyjnego. Wózki widłowe, wszechstronne konie robocze krajobrazu przemysłowego, odgrywają kluczową rolę w obsłudze materiałów w zakładach produkcyjnych. W tej części raportu przedstawiamy kompleksową analizę różnych typów wózków widłowych, badając ich unikalne cechy, zastosowania i korzyści w optymalizacji przepływu materiałów w środowisku produkcyjnym.
Wózki widłowe są niezbędnymi narzędziami w produkcji, oferującymi różnorodne rozwiązania spełniające określone potrzeby w zakresie obsługi materiałów. Analizujemy wiele dostępnych typów wózków widłowych, odnosząc się do ich zróżnicowanych możliwości, zastosowań i wpływu, jaki mają na wydajność operacyjną.
Wózki widłowe z przeciwwagą
Powszechnie znane ze swojej stabilności i wszechstronności, wózki widłowe z przeciwwagą są końmi roboczymi w transporcie materiałów. Dzięki różnym konfiguracjom, w tym konstrukcjom trójkołowym i czterokołowym, doskonale sprawdzają się w zadaniach załadunku i rozładunku, co czyni je niezbędnymi w ogólnych zastosowaniach produkcyjnych.
Wózki wysokiego składowania
Zaprojektowane z myślą o wąskich korytarzach magazynowych, wózki wysokiego składowania zapewniają niezrównaną zwrotność i zasięg pionowy. Ich zdolność do podnoszenia ładunków na znaczne wysokości sprawia, że idealnie nadają się do przechowywania i pobierania w magazynach produkcyjnych o dużej gęstości.
Wózki do kompletacji zamówień
Dostosowane do wydajnej realizacji zamówień, wózki do kompletacji zamówień umożliwiają operatorom podnoszenie ładunku w celu dokładnego i szybkiego wyboru pozycji. Te wózki widłowe odgrywają kluczową rolę w zakładach produkcyjnych koncentrujących się na kompletacji i dystrybucji zamówień.
Podnośniki paletowe
Kompaktowe i zwrotne podnośniki paletowe są idealne do transportu towarów na paletach na krótkich dystansach. Przyczyniają się do usprawnienia procesów produkcyjnych, zwłaszcza w obszarach o ograniczonej przestrzeni.
Wózki widłowe terenowe
Gdy produkcja wykracza poza magazyn do środowisk zewnętrznych, do gry wkraczają wózki widłowe do pracy w trudnym terenie. Te wytrzymałe maszyny radzą sobie z nierównymi powierzchniami i trudnymi terenami, wspierając prace budowlane i produkcyjne na zewnątrz.
Ładowarki teleskopowe
W przypadku zakładów produkcyjnych o zróżnicowanych potrzebach, ładowarki teleskopowe oferują większy zasięg i wszechstronność. Te wózki widłowe są w stanie obsługiwać różne osprzęty, dzięki czemu nadają się do szerokiego zakresu zadań związanych z transportem materiałów.
Pojazdy sterowane automatycznie (AGV)
Wykorzystując automatyzację, wózki AGV są futurystycznym rozwiązaniem dla logistyki produkcji. Te samojezdne wózki widłowe zwiększają wydajność, poruszając się po wcześniej zdefiniowanych ścieżkach, przyczyniając się do trwającego trendu inteligentnej produkcji.
Elektryczne wózki widłowe
Wraz z rosnącym naciskiem na zrównoważony rozwój, elektryczne wózki widłowe zyskują na popularności. Ich cicha praca, zerowa emisja spalin i niższe koszty operacyjne sprawiają, że są one opłacalnym wyborem dla zakładów produkcyjnych dbających o środowisko.
Podsumowując, zróżnicowany krajobraz wózków widłowych oferuje producentom spektrum opcji dostosowania procesów transportu materiałów do ich konkretnych potrzeb. Rozumiejąc charakterystykę i zastosowania różnych typów wózków widłowych, zakłady produkcyjne mogą podejmować świadome decyzje w celu zwiększenia wydajności, bezpieczeństwa i ogólnej doskonałości operacyjnej. Niniejszy raport służy jako przewodnik do poruszania się po bogatym gobelinie opcji wózków widłowych dostępnych w dążeniu do płynnej obsługi materiałów w środowiskach produkcyjnych.
Wnioski: przekształcanie krajobrazów obsługi materiałów w produkcji
W skomplikowanym tańcu materiałów w sferze produkcyjnej optymalizacja wewnętrznych systemów transportowych stanowi podstawę sukcesu operacyjnego. Niniejszy raport skrupulatnie poruszał się po wieloaspektowym krajobrazie obsługi materiałów, badając kluczowe role odgrywane przez systemy przenośników taśmowych, zautomatyzowane pojazdy sterowane (AGV), autonomiczne roboty mobilne (AMR) i szereg typów wózków widłowych. Wraz z ciągłą ewolucją krajobrazu produkcyjnego, zmieniają się również dostępne narzędzia do organizowania płynnego przepływu materiałów.
Raport pokazuje kluczową rolę, jaką odgrywają systemy transportu wewnętrznego w organizacji nowoczesnych operacji produkcyjnych. Gdy systemy przenośników taśmowych przechodzą przez linie produkcyjne, pojazdy AMV i AMR poruszają się po hali produkcyjnej, a wózki widłowe precyzyjnie podnoszą, przenoszą i umieszczają materiały, synergia tych technologii kształtuje krajobraz operacyjny zdefiniowany przez wydajność, bezpieczeństwo i zdolność adaptacji. Spostrzeżenia przedstawione w raporcie służą jako kompas, prowadzący podmioty produkcyjne przez zawiłości logistyki wewnętrznej, oferując plan wykorzystania pełnego potencjału systemów transportu bliskiego w dążeniu do doskonałości operacyjnej. W ciągłej ewolucji produkcji, wybory dokonywane w transporcie materiałów będą nadal rezonować, kształtując fabryki jutra.