Przy rosnącej złożoności produkcji i związanych z nią zapasów magazynowych coraz większym wyzwaniem dla przedsiębiorstw stają się zagadnienia intralogistyczne. To, w jaki sposób zorganizowany jest transport wewnętrzny oraz przepływ materiałów w magazynie, bezpośrednio wpływa bowiem na efektywność. Warto więc pomyśleć o optymalizacji systemów składowania, która nie tylko usprawni ruch, ale także zwiększy wydajność.
Kontrola ruchu, a więc zapewnienie pełnej sprawności wykorzystywanych maszyn i urządzeń, to bardzo ważne zagadnienie we współczesnych zakładach produkcyjnych. Określa bowiem zdolność firmy do wykonywania zadań, a w efekcie także terminowej produkcji i dotrzymywania zobowiązań. Proces zapewnienia sprawnego ruchu zaczyna się jednak nie na linii produkcyjnej, ale już od chwili wpłynięcia poszczególnych komponentów do magazynu. Na płynny przepływ materiałów mają wpływ urządzenia związane z ich obróbką oraz te, które pomagają je efektywnie składować i przenosić. Właśnie dlatego optymalizacja logistyki wewnętrznej to jedno z zagadnień, które cieszy się obecnie dużym zainteresowaniem wśród przedsiębiorców.
Automatyzacja transportu i minimalizacja powierzchni
Myśląc o efektywnej kontroli ruchu, warto zastanowić się nad kluczowymi obszarami, które mogą wpływać na wydajność samych magazynów. Do najważniejszych z nich należą przede wszystkim transport wewnętrzny oraz odpowiednie wykorzystanie powierzchni magazynowej.
W kontekście pierwszego zagadnienia dotychczas większość polskich przedsiębiorstw w dużej mierze opierała się na wykorzystywaniu wózków widłowych. Okazuje się jednak, że warunki lokalowe magazynów z dużą ilością różnego rodzaju elementów często komplikują kwestie związane z poruszaniem się wielu wózków. Doskonałym przykładem może być składowanie i transport wszelkiego rodzaju elementów długich. Istnieją jednak rozwiązania, które mogą też sprostać tym wyzwaniom. Mowa o zautomatyzowanych systemach z zakresu Przemysłu 4.0, takich jak suwnice czy podnośniki, które pozwalają na znacznie szybszy transport wewnętrzny.
Tego typu systemy mogą również pomóc w optymalizacji dotyczącej drugiej kwestii, a zatem powierzchni magazynu. Okazuje się, że wciąż wiele przedsiębiorstw składuje materiały na ziemi – nie wykorzystując tym samym przestrzeni rozciągającej się aż do sufitu. Niektóre z nich decydują się nawet na budowę kolejnej hali, nie wiedząc, że wyposażenie dotychczasowej w zautomatyzowane systemy składowania mogłoby okazać się o wiele lepszym wariantem kosztowym. Inwestycja w automatyczne, zaprojektowane na miarę regały, charakteryzujące się bardzo wysoką gęstością składowania, jest bardziej ekonomicznym rozwiązaniem, niż budowa bądź dzierżawa dodatkowego magazynu.
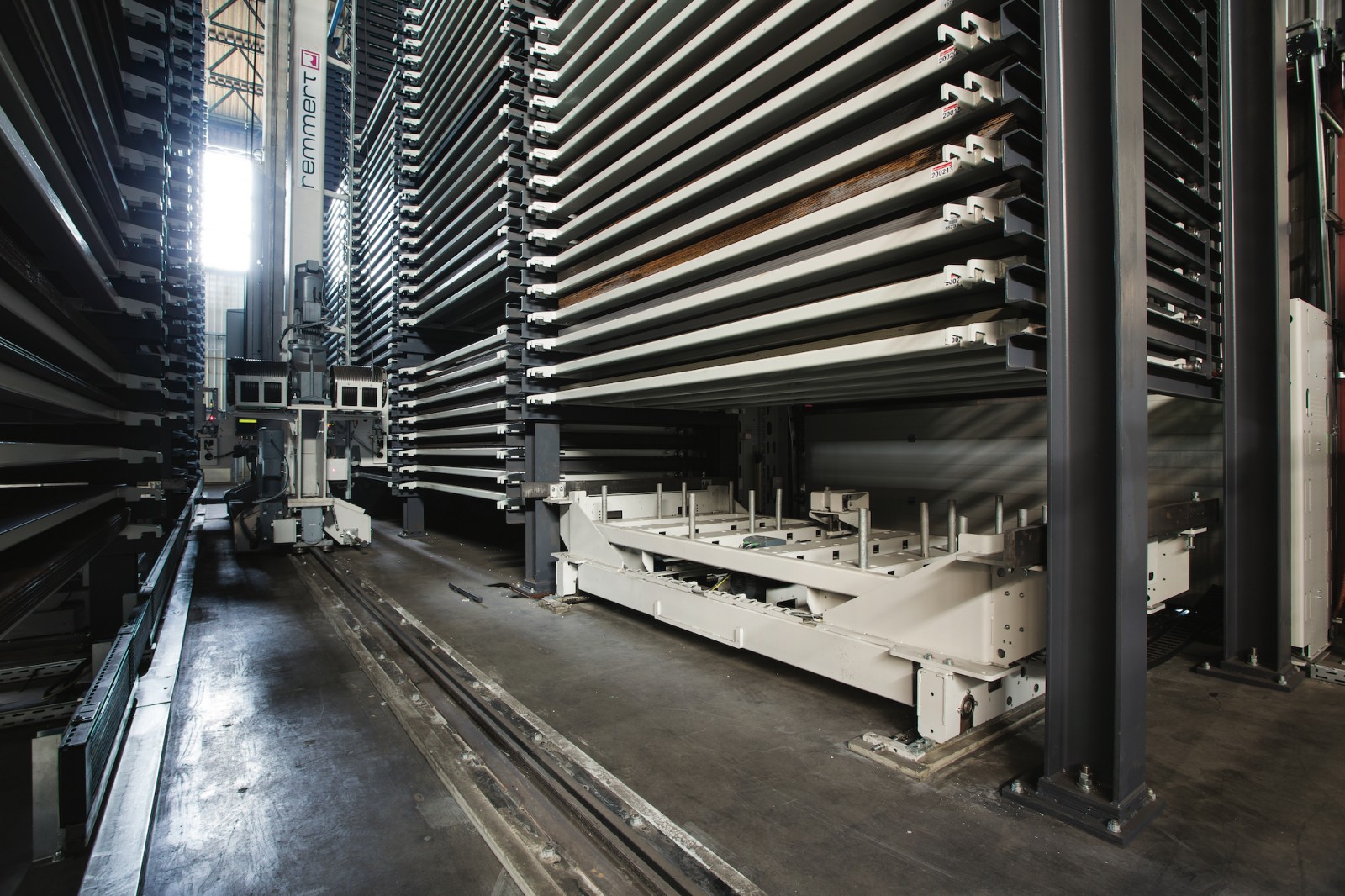
Niezależność od producenta i modułowa budowa
Optymalizacja transportu i składowania to tylko niektóre z zalet automatycznych systemów magazynowych. Wspierają one także dalsze procesy produkcyjne, pomagając w kompletacji zamówień i podawaniu materiałów do maszyn obróbczych. Jest to szczególnie ważne w kontekście wykorzystania potencjału tych maszyn i kontroli ich ruchu.
Wciąż w wielu zakładach produkcyjnych nowoczesne urządzenia, np. do cięcia laserowego, nie są w pełni obciążone. Bez względu na to, jak trwałe i wydajne są maszyny – jeśli otoczenie produkcyjne nie jest kompatybilne, proces nie przebiega płynnie, a w efekcie mogą zdarzać się kosztowne przestoje. Przepływ materiału ma ogromne znaczenie dla sprawności procesu produkcji. Opóźnienia mają negatywny wpływ na wydajność. Przykładowo, jeśli w zakładzie przetwarzania blach każda paleta musi podjeżdżać do lasera osobno, a następnie każda z blach przekładana jest na stół ręcznie, wykorzystanie urządzenia oscyluje na poziomie zaledwie 25%. W takim przypadku wysoki nakład inwestycyjny przeznaczony na zakup lasera przestaje być opłacalny. W przypadku gdy urządzenia do cięcia laserowego są zintegrowane z automatyzacją we wzajemnie skoordynowanej koncepcji przepływu materiałów, wykorzystanie maszyn można podnieść nawet do 80%. Co więcej, tego typu rozwiązania zmniejszają także ryzyko uszkodzenia materiałów, a zatem ograniczają koszty.
Eksperci zwracają uwagę w szczególności na takie systemy automatyzacji, które można elastycznie podłączyć do maszyn w różnym wieku, pochodzących od różnych producentów. Gwarantują one, że urządzenia zewnętrzne mogą być w łatwy sposób wymieniane, niezależnie od tego, od jakiego producenta pochodzą. Jest to ważne z uwagi na fakt, że maszyny te mają krótszą żywotność niż podłączona do nich automatyka. Mowa tu o różnego rodzaju maszynach obróbczych: laserach, wykrawarkach, prasach, maszynach do cięcia – systemy załadunku i rozładunku, które są kompatybilne z każdym urządzeniem, zapewniają maksymalne bezpieczeństwo inwestycji.
Zautomatyzowane rozwiązanie przepływu materiałów powinno być również modułowe. Jest to ważne szczególnie dla przedsiębiorstw, które planują rozbudowę magazynów czy linii produkcyjnych. W przypadku modułowej budowy, niezależnie od tego, jak szybko nadejdzie taka potrzeba, kolejne elementy będą mogły zostać w prosty sposób zintegrowane z już istniejącym systemem. Modułowość wraz z niezależnością od producenta są cechami, dzięki którym automatyka pozwala na stworzenie wysoko wydajnej inteligentnej fabryki.
Intuicyjne oprogramowanie
Kontrola ruchu w odniesieniu do wszystkich elementów produkcji to korzyść strategiczna. Jednak nawet najlepsza automatyzacja na niewiele się zda, gdy brakuje niezbędnych informacji do wydajnego i sprawnego przepływu materiałów lub są one nieprawidłowo wykorzystywane. Warto więc postawić także na prosty i intuicyjny w obsłudze system oprogramowania i sterowania całym procesem produkcyjnym. Tego typu rozwiązania obejmują procesy od zarządzania magazynem aż do kierowania produkcją. Zapewniają maszynom zaopatrzenie w materiał i zajmują się przyjęciem obrobionych części do magazynu. Niektóre systemy oprogramowania sterują i optymalizują magazyny oraz podłączają zewnętrzne jednostki produkcji, które można obsługiwać ręcznie bądź w sposób w pełni lub połowicznie zautomatyzowany. Dzięki temu różne maszyny do obróbki mogą być bezpośrednio połączone z magazynem, aby za pośrednictwem interfejsów danych wywoływać stamtąd materiał lub przyjmować części po obróbce.
Jednym z wyzwań może się okazać integracja nowego oprogramowania z istniejącą strukturą systemów. Przed wyborem dostawcy dobrze więc zwrócić uwagę, czy istnieje taka możliwość. Dzięki temu oprogramowanie będzie stanowić wsparcie dla użytkowników podczas sprawnej pracy łańcucha procesowego pomiędzy produkcją a logistyką. Dobrze byłoby, by system posiadał również funkcje zarządzania użytkownikami i uprawnieniami, a także udostępniał informacje o statusie, tak by zarządzać danymi materiałów i magazynu.
Podobnie jak w systemach automatyzacji, tak samo w przypadku oprogramowania cenna może się okazać jego modułowa budowa. Pozwoli ona szybko i sprawnie rozwijać istniejące już systemy. Ponadto skonstruowane w prosty i intuicyjny sposób oprogramowanie sprawia, że jest łatwe do wdrożenia i wymaga krótkiego czasu przeszkolenia pracowników. Tego typu wdrożenie może pomóc w nieskomplikowany sposób zarządzać stanami magazynowymi i ich korektami, wpływając na poprawę przepływu materiałów.

Rozwiązania dla dużych i małych
Mimo zalet zautomatyzowanych systemów magazynowych wiele firm produkcyjnych wciąż nie decyduje się na ich wdrożenie, sądząc, że tego typu zastosowania są opłacalne tylko w dużych czy średnich przedsiębiorstwach. Wiąże się to z przekonaniem, że kontrola ruchu ma sens ekonomiczny tylko w przypadku powtarzalnej produkcji na szeroką skalę.
Jest to jeden z powszechnych mitów, które powstały wokół systemów automatyzacji. Okazuje się bowiem, że wszelkie wymienione przykłady rozwiązań usprawniających przepływ materiałów nie tylko mają zastosowanie w mniejszych firmach, ale przede wszystkim właśnie im mogą przynieść wymierne korzyści. Przy produkcji krótkich serii automatyzacja pozwalająca na podniesienie wydajności urządzeń takich jak np. lasery jest szczególnie ważna. Zakup tego typu maszyny jest bowiem kosztowny i może wiązać się ze znacznym nakładem środków, który będzie bardziej odczuwalny dla mniejszego przedsiębiorcy. Optymalizacja wynikająca z wdrożenia rozwiązań do automatyzacji – od transportu wewnętrznego, przez przestrzeń magazynową, procesy produkcyjne, aż po oprogramowanie – daje szybszy zwrot z inwestycji, także tych związanych z zakupem urządzeń zewnętrznych (maszyn, wykrawarek, laserów itp.). Usprawnienie przepływu materiałów również w małych zakładach i magazynach może się okazać dla nich kluczowe dla osiągnięcia efektywności.
Automatyzacja, a także wiążąca się z nią cyfryzacja, zapewniają firmie perspektywę tworzenia wyższej wartości na bazie kompleksowej strategii kontroli ruchu. Wydajna produkcja zawsze opiera się na indywidualnie zaplanowanym procesie, także tym związanym z przepływem materiałów. Właśnie dlatego każde przedsiębiorstwo przed zakupem maszyn powinno się skonsultować z niezależnym specjalistą ds. przepływu materiałów. Warto postawić na optymalne rozwiązania, które usprawnią intralogistykę i będą wspierać firmę w długofalowej perspektywie. Modułowa budowa i niezależność od producentów maszyn, zarówno w przypadku systemów automatyzacji, jak i oprogramowania, sprawią, że przedsiębiorstwa będą mogły szybko się rozwijać.
Paweł Zieliński jest dyrektorem generalnym firmy Remmert w Europie Wschodniej.