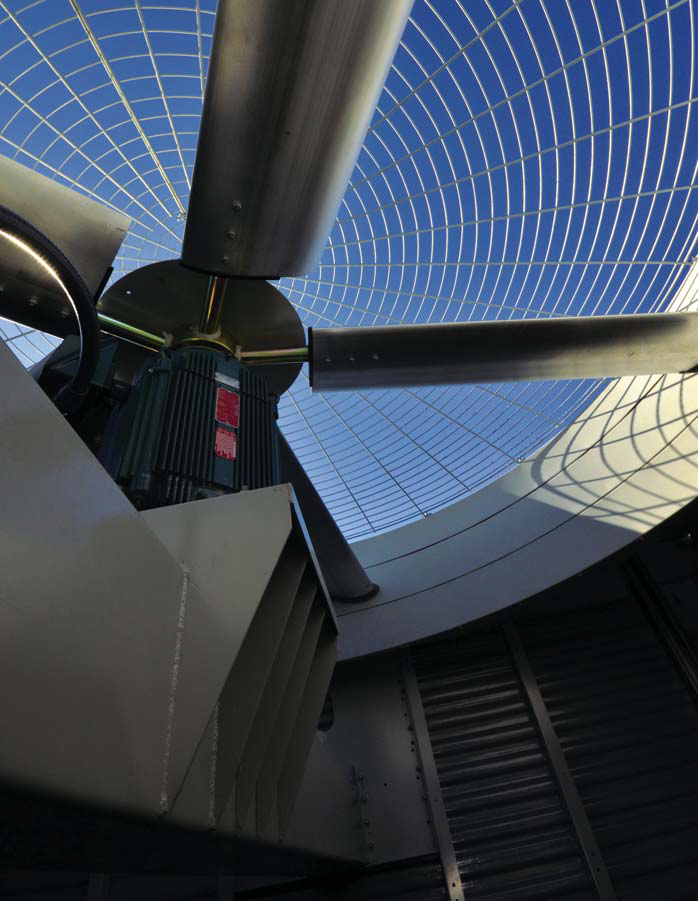
Regulatory częstotliwości (ang. variable frequency driver – VFD), zwane też powszechnie falownikami, często wykorzystywane są w celu obniżenia kosztów eksploatacji pomp, wentylatorów, sprężarek oraz innych urządzeń o zmiennym obciążeniu, stosowanych w różnych budynkach.
Mimo powszechnej obecności silników w wielu projektowanych systemach infrastruktury budynkowej i tego, że często w znacznym stopniu odpowiadają one za profil zużycia energii w budynku, zwykle myśli się o nich na samym końcu. Według tradycyjnego podejścia projekty infrastruktury mechanicznej, instalacji elektrycznej, wodno-kanalizacyjnej oraz systemów ochrony przeciwpożarowej budynków skupiały się przede wszystkim na aspektach zdrowia/bezpieczeństwa, funkcjonalności oraz początkowych kosztów kapitałowych. Jednakże wprowadzenie bardziej restrykcyjnych przepisów i norm w zakresie efektywności energetycznej przyczyniło się do zwiększenia nacisku na to, aby przy projektowaniu tego typu instalacji i podsystemów uwzględniać w znacznie większym stopniu aspekt energooszczędności.
Wielu właścicieli budynków wolałoby poprzestać na projektach, które spełniają w minimalnym zakresie wymagania przepisów, ale nowoczesnym i proaktywnym inżynierom oraz projektantom powinno zależeć na podkreśleniu konieczności zrozumienia, w jaki sposób komponenty infrastruktury zużywają energię i jak można zoptymalizować ich parametry i warunki pracy bez naruszania tradycyjnych wartości projektowych. Czasem indywidualne komponenty instalacji mogą stanowić technologiczne „ślepe zaułki”, bez perspektyw na dalszy rozwój, co może wymagać znalezienia innych energooszczędnych rozwiązań.
Wszechobecne silniki
Według większości metod projektowania podstawowym celem jest znalezienie rozwiązania najkorzystniejszego cenowo – priorytetem jest wysoka wydajność za niską cenę. Pytanie brzmi: jaki czynnik w projektach powoduje największe zużycie energii? Często są nim właśnie silniki – to one stanowią ukryte źródło poboru energii w większości analizowanych kategorii zużywania energii w budynkach komercyjnych.
Ujmując to szerzej, układy napędzane silnikami elektrycznymi odpowiadają za ponad jedną trzecią łącznego zapotrzebowania na energię elektryczną w Stanach Zjednoczonych oraz za 43% do 46% w ujęciu globalnym, według danych statystycznych Międzynarodowej Agencji Energetycznej. Całkowity pobór energii przez silniki w sektorze przemysłowym przewyższa zużycie w sektorze komercyjnym w stosunku ok. 3:1. Z łącznej ilości energii zużywanej przez silniki na całym świecie ok. 68% wykorzystywane jest przez silniki o średniej mocy z zakresu 1-360 kW, który obejmuje ogromną część silników wykorzystywanych w infrastrukturze budowlanej.
Wartość sprawności energetycznej
W przypadku większości zastosowań koszt eksploatacji radykalnie przewyższa koszt samego silnika w całym cyklu użytkowania. Niestety, w typowych instalacjach budynków zazwyczaj dopasowuje się wielkość mocy silnika do największych obciążeń, które zwykle stanowią tylko niewielki procent łącznej liczby godzin jego pracy. Jeśli taki silnik miałby pracować na pełnych obrotach, bez względu na wielkość obciążenia, straty energii byłyby ogromne. Na podstawie prostych zależności i praw wynikających z teorii maszyn elektrycznych wiadomo, że wartość mocy jest proporcjonalna do wartości prędkości obrotowej zgodnie ze wzorem na obciążenia odśrodkowe:
P2[kW] = P1[kW] (ω2[obr./min]/ω1[obr./min])3
Z tego wzoru wynika, że jeśli można zastosować do danego obciążenia niższą prędkość, wtedy można znacząco zmniejszyć moc, jaką musi wytworzyć silnik.
Do przedstawienia tej zależności posłużymy się przykładem z uproszczonym profilem obciążenia i silnikiem o mocy 5,5 kW i prędkości 1800 obr./min (tabela 1). Jeśli średnia prędkość wymagana przez teoretyczne obciążenie wynosiłaby 75% prędkości przy pełnym obciążeniu, wtedy średnia wartość wymaganej mocy wynosiłaby 2,3 kW. Posługując się kosztami urządzenia podanymi przez dystrybutora urządzeń elektrycznych, specjalizującego się w silnikach indukcyjnych i regulatorach VFD, oraz przyjmując definicje kilku zmiennych, jak koszt energii elektrycznej przypadający na kWh oraz liczba godzin pracy, możemy uzyskać przybliżone zestawienie kosztów sprzętu wraz z z kosztami energii elektrycznej oraz zwrotem z inwestycji.
Podane zmienne mają charakter uogólniony, a zużycie w indywidualnych przypadkach może się różnić w zależności od poszczególnych parametrów roboczych obciążenia oraz kosztu energii elektrycznej w danym kraju. Ponieważ z przedstawionej zależności wynika, że moc silnika nie zależy liniowo od prędkości obrotowej, błędem jest twierdzenie, że obliczenia oparte na średniej prędkości profilu obciążenia będą precyzyjnie określać całkowite zużycie energii (chyba że przez zdecydowaną większość czasu mamy do czynienia z takim obciążeniem przy takiej średniej prędkości obrotów). Jednakże podany przykład miał zilustrować fakt, że koszty energii elektrycznej zazwyczaj stanowią decydujący czynnik przy rozważaniach o zastosowaniu zaawansowanych układów regulacji prędkości silnika.
Sprawność silników indukcyjnych AC
Wielofazowe silniki indukcyjne prądu przemiennego (AC) tradycyjnie dominują w branży silników elektrycznych.
Aby zrozumieć pojęcie sprawności silnika, należy najpierw poznać przyczyny strat energii. Straty można podzielić na cztery podstawowe kategorie:
- straty elektryczne – straty w przewodzeniu prądu I2R w stojanie i wirniku, które rosną gwałtownie wraz ze wzrostem natężenia prądu. Można je ograniczyć przez zmniejszenie rezystancji uzwojenia stojana i klatki wirnika;
- straty magnetyczne – histereza/prąd wirowy w pakiecie blach ze stali. Można je ograniczyć przez ulepszenie procesów metalurgicznych przy wytwarzaniu stali;
- straty mechaniczne – tarcie w układach łożysk, obciążenia pasożytnicze, jak chłodzące wentylatory w silnikach budowy zamkniętej chłodzonych wentylatorami (TEFC) itp.;
- dodatkowe straty obciążeniowe – rozproszenie/nieregularności strumienia magnetycznego w szczelinie powietrznej pomiędzy wirnikiem i stojanem. Można je ograniczyć przez zwiększenie precyzji procesu produkcji.
Spośród opisanych rodzajów strat najbardziej znaczące są tzw. straty na ciepło I2R. Można je zaobserwować w postaci zwiększonego wytwarzania ciepła. Zatem przeciwdziałanie powstawaniu tych strat pośrednio może wpłynąć na straty spowodowane przez wentylację silnika w konstrukcjach TEFC.
Wszystkie silniki indukcyjne mają podstawową prędkość (prędkość synchroniczna), która jest proporcjonalna do liczby biegunów magnetycznych w konstrukcji silnika (zwykle 2–8) oraz częstotliwości źródła zasilania (tabela 2).
Jednakże prędkość wirnika jest zawsze nieznacznie opóźniona względem prędkości wirującego pola magnetycznego w stojanie. Ta różnica pomiędzy prędkością synchroniczną i rzeczywistą prędkością wirnika nazywana jest „poślizgiem”. Zmniejszenie rezystancji stojana i wirnika powoduje mniejsze straty I2R, ale jednocześnie zmniejsza poślizg. Niestety, poślizg bezpośrednio wiąże się z wielkością momentu obrotowego, który może wytworzyć silnik o danej konstrukcji. W związku z tym obciążenia o wysokiej bezwładności, które wymagają większego momentu rozruchowego, zwykle stwarzają konieczność zastosowania silników wykonanych według norm NEMA o niższej sprawności (tabela 3). Konstrukcje stojanów z niższymi stratami I2R również zwykle mają wyższy początkowy prąd rozruchowy.
W jaki sposób można zwiększyć sprawność VFD?
Nie da się przeprowadzić powtarzalnych i ciągłych pomiarów sprawności, jeśli nie dysponuje się znormalizowaną metodą pomiaru. Straty energii w regulatorze VFD zwykle przypisuje się przewodnictwu (prąd elektryczny płynący przez urządzenie) i stratom przy przełączaniu (straty energii przy włączaniu i wyłączaniu tranzystorów podczas pracy prostownika na wejściu i falownika na wyjściu). Teoretycznie producenci falowników VFD mogą wpłynąć na sprawność układu napędowego przez optymalizację tych elementów konstrukcji VFD. W zasadzie większość producentów podaje w swoich nowszych konstrukcjach falowników VFD sprawność na poziomie ok. 95%.
Projektowanie VFD podlega dalszej ewolucji – przykładem jest wprowadzenie szóstej generacji tranzystorów bipolarnych z izolowaną bramką (IGBT), które zapewniają ok. 20% względnego zmniejszenia strat przy przełączaniu w porównaniu z wcześniejszymi konstrukcjami IGBT. Jednak nadal trudno jest inżynierom, którzy wykonują projekty techniczne, dokładnie obliczyć ilościowy wpływ tych konstrukcji na sprawność ogólną całego układu. Bezpośrednie zestawienia podzespołów różnych producentów mają jedynie charakter teoretyczny, jeśli nie dysponuje się rzetelnymi znormalizowanymi metodami pomiarowymi.
Mimo że podawana przez producentów VFD wartość sprawności umożliwia przybliżoną ocenę szacunkową sprawności układu silnik-VFD, duża liczba zmiennych może wpłynąć na rzeczywistą sprawność takiego układu. Przykładem takich zmiennych są: częstotliwość nośna, z którą pracuje silnik, czy też typ zastosowanej konstrukcji silnika NEMA.
Najlepszym sposobem, aby uzyskać wzrost sprawności układu, jest skupienie się na kluczowych kwestiach:
- poznaniu charakterystyki prędkości i momentu obrotowego obciążenia,
- poznaniu całkowitego profilu obciążenia/cyklu pracy,
- wyborze sprzętu o odpowiednich parametrach, który będzie spełniać wymagania projektowe,
- regulacji układu, aby wykonywał tylko zadaną pracę.
Odkrywanie koła na nowo z silnikami PMAC
Choć nowe normy dotyczące sprawności układów napędowych popchnęły rozwój silników indukcyjnych w kierunku jeszcze większej sprawności, to jednak z każdą nową normą obserwuje się coraz mniejsze uzyski ilościowe w zakresie wzrostu efektywności. Dalsza poprawa nadal jest możliwa, ale w pewnym momencie może już nie być uzasadniona pod względem ekonomicznym, jeśli nie będzie bazowała na jakiejś znaczącej innowacji technologicznej. Biorąc to pod uwagę, silniki indukcyjne mogą się zbliżać do ewolucyjnego końca, bez szans na dalsze perspektywy ulepszeń. Niemniej jednak możliwe jest, aby inne, podobne technologie zastąpiły silniki indukcyjne, podobnie jak regulatory VFD pojawiły się jako tzw. destabilizująca innowacja w sektorze systemów ogrzewania, wentylacji i klimatyzacji (HVAC).
Do najnowszych rozwiązań należą silniki prądu przemiennego z magnesem trwałym (PMAC). Silniki PMAC nazywane są również synchronicznymi silnikami AC lub bezszczotkowymi silnikami DC. Silniki te niekoniecznie można nazwać nowymi, ale jeszcze do niedawna w ogóle nie były stosowane w sektorze HVAC. Tradycyjnie używano ich tylko w sytuacjach, gdzie wymagana była precyzyjna regulacja niskiej prędkości i momentu obrotowego, zatem ich funkcje pokrywają się z funkcjonalnością silników indukcyjnych z wektorowym sterowaniem VFD. Ich wyższy koszt w porównaniu z typowym układem silnik indukcyjny/VFD ograniczył udział silników PMAC na rynku systemów budowlanych. Niemniej jednak korzyści płynące z funkcjonalności silników PMAC zostały wykorzystane przynajmniej przez jednego producenta chłodni kominowych, który użył ich w swoim najlepszym modelu chłodni, zawierającym przepływowe wentylatory chłodzące o dużej średnicy. Producent ten wykorzystał charakterystykę wydajności silników PMAC przy niskiej prędkości obrotowej i wyeliminował problematyczne wentylatory z napędem pasowym/przekładniami redukcyjnymi, które zazwyczaj spotyka się w takich konstrukcjach. Tym sposobem mechaniczna konstrukcja komina została znacznie uproszczona, a zlikwidowanie mechanizmu mechanicznej redukcji prędkości bardzo znacząco poprawiło całkowitą sprawność układu. Takie zastosowanie, w którym prędkość robocza obciążenia jest krańcowo niższa od standardowej prędkości podstawowej silnika indukcyjnego (1800 obr./min, 3600 obr./min itp.) i gdzie nie są już wymagane napędy pasowe lub przekładnie mechaniczne, ilustruje sytuacje i aplikacje, do których ten silnik będzie znakomicie pasować.
W przypadku silników o mniejszej mocy (7,5 kW lub mniej) poprawa sprawności, będąca nieodłącznym aspektem konstrukcji PMAC, kompensuje ich wyższy koszt w porównaniu z silnikami indukcyjnymi. Zwiększenie całkowitej sprawności może wynosić 2% w stosunku do silników indukcyjnych NEMA Premium. Jednakże sprawność silników PMAC jest najbardziej widoczna przy niższych prędkościach obrotowych, gdyż wtedy różnica w całkowitej sprawności może nawet przewyższać 20%. W połączeniu ze współczynnikiem regulacji prędkości 1000:1 lub 2000:1, typowym dla silników PMAC wykorzystywanych ze sterowaniem wektorowym, stanowią one doskonały wybór do zastosowań, gdzie nie da się uniknąć regularnej pracy na niskich obrotach.
Podstawowe zasady działania są takie same w przypadku silników indukcyjnych i PMAC. Wirujące pole magnetyczne w stojanie oddziałuje na wirnik, a prędkość wirnika dyktowana jest przez liczbę biegunów magnetycznych i częstotliwość źródła zasilania podłączonego do stojana.
W rzeczywistości stojan w silniku PMAC jest dokładnie taki sam jak w silniku indukcyjnym. Najważniejsza różnica tkwi w wirniku. Zamiast klatki i pakietu blach stalowych, jak w wirniku silnika indukcyjnego AC, wirnik w silniku PMAC wykorzystuje mocne magnesy ziem rzadkich, przymocowane na stałe do pakietu blach ze stali.
W ten sposób powstaje w wirniku stałe pole magnetyczne o stałej sile, zamiast indukowanego pola magnetycznego charakterystycznego dla silników indukcyjnych. Rozwiązanie to można nazwać mieczem obosiecznym, ponieważ siła pola magnetycznego wirnika utrzymuje się na stałym poziomie bez względu na zmianę prędkości silnika.
Wracając do strat energii, w silniku indukcyjnym straty I2R są największe. W przypadku silników PMAC również występują straty I2R związane z uzwojeniem stojana, jednak ponieważ wirujące pole magnetyczne stojana bezpośrednio oddziałuje na magnesy w wirniku, straty I2R (ciepło) związane ze wzbudzaniem prądu w wirniku są nieznaczne. Takie praktyczne wyeliminowanie strat I2R wirnika poprzez zastosowanie trwałych magnesów znacząco obniża całkowitą sumę strat. Niestety, magnesy mogą utrudniać rozruch silnika, a po jego uruchomieniu mogą działać jak generator i powodować powstanie „wstecznej siły elektromotorycznej” (EMF).
Sterowanie silnikiem PMAC może być skomplikowane. Magnesy w wirniku łatwo ustawią się w jednej pozycji i będą się opierać innym pozycjom. Zatem gdy wirnik będzie rozwijać moment obrotowy, ustawiając się w odpowiedniej pozycji w stosunku do danego uzwojenia stojana, pozostałe uzwojenia nie rozwiną tej samej wielkości momentu obrotowego. W rzeczywistości, zależnie od lokalizacji kąta obrotowego wirnika działającego na konkretne uzwojenie, moment rozwijany przez to uzwojenie może być ujemny i przeciwdziałać obrotom zgodnym silnika. Rozwiązaniem jest natychmiastowe „wyłączenie” tego uzwojenia, gdy względna pozycja wirnika może utworzyć ujemny moment obrotowy. Ponadto po uruchomieniu silnika w miarę wzrostu siły wirującego pola elektromagnetycznego w stojanie może ona nie wystarczyć, aby bez szarpnięcia pokonać siły przyciągania trwałych magnesów działających na stalową strukturę stojana. Z tego względu silniki PMAC wymagają użycia regulatorów VFD, aby sterować wejściowym natężeniem prądu podłączonego do uzwojenia stojana. Z tym również wiąże się to, że silniki PMAC nie są samouruchamiające się – nie można ich uruchomić za pomocą standardowego rozrusznika.
Ważną kwestią związaną z silnikami PMAC jest to, że obecność trwałego magnesu w wirniku powoduje, iż silnik będzie działać jako generator energii elektrycznej. Przy szybszych obrotach wirnika nastąpi wzrost generowanego napięcia, który zacznie przeciwdziałać zewnętrznemu napięciu zasilającemu stojan. Zjawisko to jest znane jako wsteczna siła elektromotoryczna EMF i może mieć zarówno zalety, jak i wady. Wsteczna siła EMF jest wprost proporcjonalna do prędkości, więc jeśli można ją jakoś zmierzyć, wtedy będzie informować o wielkości prędkości wirnika, bez konieczności stosowania przetwornika obrotowego. Jeśli prędkość wirnika jest znana, można wtedy precyzyjnie nadzorować prędkość i moment obrotowy silnika (tj. bezczujnikowe sterowanie wektorowe). Jednakże przy wyższych prędkościach generowane napięcie będzie dalej rosło i ograniczało maksymalną teoretyczną prędkość silnika. Inną kwestią, na którą należy zwrócić uwagę, jest to, że w miarę jak silnik zwalnia bez przyłożonego napięcia zasilającego, generowane napięcie będzie zasilać zaciski silnika i stanowić potencjalne zagrożenie porażeniem prądem elektrycznym.
Autor: John Yoon jest starszym inżynierem elektrykiem w firmie McGuire Engineers. Ma 20-letnie doświadczenie w projektowaniu systemów rozdzielczych energii elektrycznej.